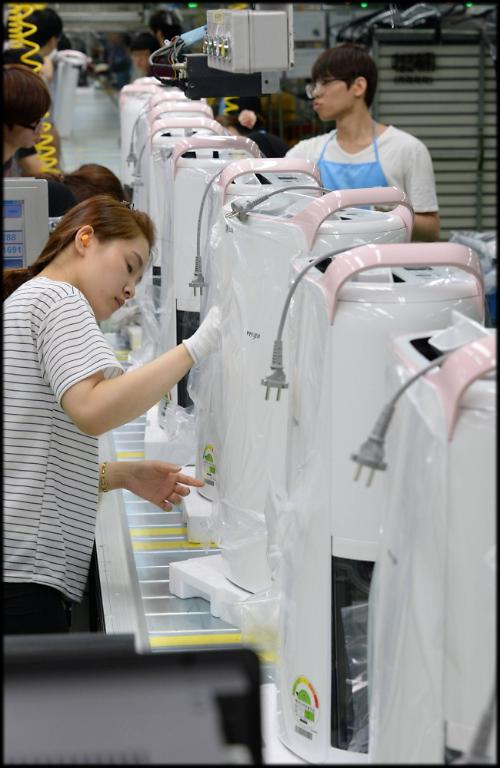
18일 경남 창원시 성산구 성산동에 위치한 LG전자 창원2공장 제습기 생산라인에서 작업자가 제품을 점검하고 있다. [사진=LG전자 제공]
아주경제 (창원) 이혜림 기자 = 지난 18일 오후 1시께 찾은 경남 창원시 성산구 성산동 LG전자 창원2공장 가정용에어컨(RAC) 생산라인(A2동)은 연중 최대 성수기를 맞아 매우 분주한 모습이었다.
공장 내부로 들어서니 오른쪽 컨베이어 벨트 위로 LG전자 주력 모델인 손흥민 에어컨으로 변신을 앞둔 철판시트가 바쁘게 움직이고 있었다. 철판시트는 열 교환기를 장착한 후 각종 전선과 PCB 등의 조립 과정, 전수검사를 거쳐 완제품의 모습으로 거듭났다.
왼 편에서는 지난해 10월 신설된 신규 생산라인에서 '휘센 칼라하라' 제습기가 생산되고 있었다. 제습기는 에어컨과 거의 동일한 과정을 거쳐 탄생된다. 이 회사는 최근 급성장하고 있는 제습기 시장을 대비해 올해 대표 모델인 '휘센 칼라하라' 제습기의 생산캐파를 기존 대비 2배 가까이 늘렸다.
창원공장 관계자는 "4·5·6월은 생산이 집중되는 시기여서 생산라인이 전쟁터와 다름없다"며 "주말도 모두 반납한 상태"라고 현장 분위기를 전했다.
대지면적 37만6900㎡(약 11.4만평)에 들어선 창원2공장의 가정용에어컨 생산라인은 '국산 제습기'의 메카다.
총 10개의 생산라인에서는 평균 15초에 한 대, 12초에 한 대꼴로 에어컨과 제습기가 만들어진다. 일부 라인은 혼류 생산이 가능하도록 설계해 제품의 수요에 따라 탄력적으로 대응하고 있다. 올해는 밀려든 제습기 주문으로 생산라인 풀가동 시점을 지난해 7월에서 4월로 앞당겼다.
바쁘게 돌아가는 생산라인이지만 '국산 제습기'라는 자부심에 걸맞게 품질관리는 철저하게 이뤄졌다.
특히 이 곳에서는 100만개 생산 제품 중 불량을 100개 이하로 줄이는 '불량률 100ppm'를 도전과제로 내걸었다.
제습기의 경우 에어컨의 실내기와 실외기가 결합돼 있어 생산공정이 까다롭고 크기가 작아 정교한 작업이 필요하기 때문에 부품 품질은 물론 조립 과정에도 더욱 신경을 써야한다는 게 회사 관계자의 설명이다.
생산라인 곳곳에는 각 공정 상황을 점검하는 체크시트와 함께 전 직원에게 적용되는 '마이머신' 시스템 등 품질경영을 위한 시스템이 구축돼 있었다. 마이머신은 자신이 담당하는 기계와 공정에 본인의 사진이 담긴 이름표를 붙여놓고 관리하는 시스템이다.
각 공정에서는 불량률을 줄이기 위해 앞사람이 한 작업을 바로 뒷 사람이 다시 한 번 더 살펴보는 '자주 순환 검사'도 진행됐다.
박재현 에어컨 생산담당 상무는 "생산라인에서 동일한 문제가 3번 발생하면 장비를 멈추는 '라인스톱제'도 운영하고 있다"며 "품질경쟁력을 최대한 끌어올리기 위해 다양한 방법을 사용하고 있다"고 설명했다.
제품 내구성 향상을 위해 부품도 국산품만 사용하고 있다. 일명 '제습기의 심장'으로 불리는 컴프레서의 경우 창원공장 내에서 직접 생산해 바로 공급한다. 그 외에 핵심부품도 모두 몇 십년간 거래하며 신뢰를 쌓은 국내 협력사의 제품을 사용한다.
오정원 LG전자 RAC 사업담당(상무)은 "요즘은 품질에 문제가 생기면 손해가 굉장히 크다"며 "중국도 기술이 많이 나아지고 있지만 오랜시간 동안 손발을 맞춰 온 국내 업체와는 비교할 수 없다. 진가는 결정적인 순간에 발휘되는 법"이라고 강조했다.
품질 향상을 위한 노력은 제품 개발 과정에서부터 지속되고 있다. 창원공장은 지난 1993년 소음진동센터를 설립하고 무향실·잔향실 등 방음 정도를 달리한 6개 실험실에서 경쟁사 제품과 자사 제품을 비교하며 소음평가를 진행해 왔다. 이곳에서는 에어컨·제습기 뿐 아니라 냉장고·세탁기 등 전 가전제품에 대한 소음연구가 이뤄진다.
윤상연 LG전자 소음진동센터 책임연구원은 "주변의 소음을 완전히 차단한 상태에서 제품의 미세한 소음까지 점검한다"며 "개발 단계에서 부터 제품이 나오기 까지 수 백번의 신뢰성 평가를 거친다"고 설명했다.
©'5개국어 글로벌 경제신문' 아주경제. 무단전재·재배포 금지