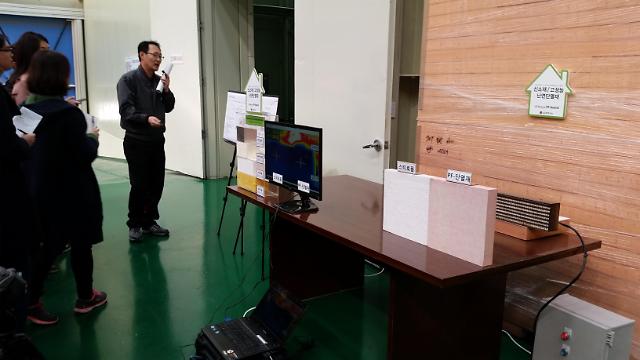
김한술 LG하우시스 PF단열재 생산기술팀장이 성능 테스트를 시연해보이고 있다.[사진=이재영 기자]
일반 소비자들은 보통 어떤 단열재를 쓸지 시공사에 맡기는 경우가 흔하다. 하지만 곰팡이 때문에 지긋지긋한 경험이 있다면 더욱 단열재를 소홀히 할 수 없다. “곰팡이는 건물 틈새가 생기게 만든 시공사의 과실이 원인일 수 있지만, 단열재의 성능 역시 무시 못한다”고 LG하우시스 관계자는 설명했다.
건축물 에너지 효율 개선의 필요성은 범지구적 환경문제 차원에서만 인식되지만, 이처럼 소소한 부분에서 생활에 밀접하게 닿아 있었다.
지난 27일 충북 청주 옥산산업단지 내에 위치한 LG하우시스의 PF(페놀폼)단열재 공장을 찾았다. 단열재가 차곡차곡 쌓여있는 공장 내부에는 쉴새없이 컨베이어벨트가 돌아가며 PF단열재를 나르고 있었다.
지난 2013년 말 총 260억원이 투자돼 완공된 생산라인에서는 연간 130만㎡의 PF단열재가 생산되고 있다. 이는 전용면적 84㎡(구 33평형) 아파트를 기준으로 약 1만3000세대에 공급할 수 있는 규모이다.
공장을 안내한 김한술 LG하우시스 PF단열재 생산기술팀장은 먼저 성능 테스트를 통해 시장 범용 단열재인 스티로폼과 PF단열재의 차이를 보여줬다. 히터를 켜서 가열하는데 스티로폼이 29도일 때 PF단열재는 23도를 나타냈다.
PF단열재는 건축 단열재 중에서 가장 높은 단열성능을 가졌다고 한다. 스티로폼보다 2배 높고 화재 발생시 일산화탄소 배출도 거의 없다는 설명이다. 김 팀장은 “PF단열재는 시공 후 25년이 지나도 성능의 90%가 유지된다”며 “우레탄은 70%, 스티로폼은 50% 이하로 떨어지는데 비해 내구성도 뛰어나다”고 부연했다.
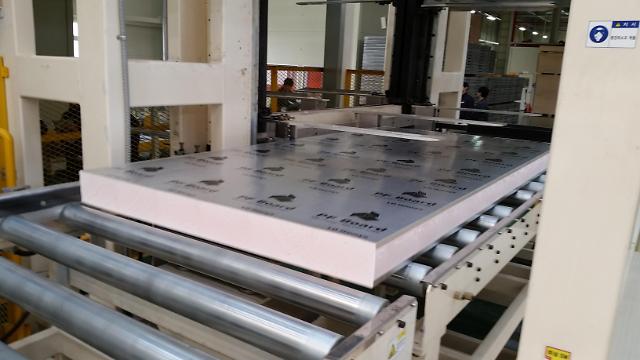
컨베이어벨트를 통과하는 PF단열재의 모습.[사진=이재영 기자]
페놀수지에 첨가되는 계면활성제, 경화제, 가소제, 면재 등 4개 원재료는 LG하우시스가 올초 국산화했다. 지난 1년여 동안 협력회사와 공동기술 개발을 통해 그간 미국, 일본, 네덜란드 등에서 전량 수입해오던 것을 100% 국산화한 것. 이 4개 첨가 원재료가 PF단열재의 제조원가에서 약 40%를 차지해 국산화를 통한 연간 10억원 가량의 제조원가 절감효과를 회사측은 기대하고 있다.
4개의 원재료가 섞여 여러 개의 노즐을 통해 슬러리 형태로 발포되고 있었다. 김 팀장은 “노즐의 형태, 숫자, 크기 등에 따라 제품의 품질격차가 생긴다”며 “이 부분에 대한 지속적인 연구개발을 통해 차별화를 시도하고 있다”고 말했다.
발포공정은 단열성능을 좌우하는 핵심공정이다. PF단열재는 이 발포공정이 까다로워 대량생산을 하기 어렵다. 따라서 세계적으로도 LG하우시스를 포함해 일본 세키스이 및 아사히카세이, 영국 킹스판 등 4개 업체만이 대량 생산을 하고 있다.
발포 공정에서 나온 제품은 컨베이어벨트를 지나면서 경화작업을 거쳐 딱딱하게 굳어졌다. 이날 만들어진 제품은 120mm 두께였다. 그 두께의 경우 양생에는 12시간이 필요하다고 한다. 이후 건조 단계를 지난 최종 제품이 공장내 빼곡하게 적재됐다.
김 팀장은 “건축물의 에너지사용량을 줄일 수 있는 자재로 주목 받으며 공장 견학 요청이 끊이지 않고 있다”며 “관심이 수요로 이어져 공장의 생산량도 계속해서 증가할 것”이라고 말했다.
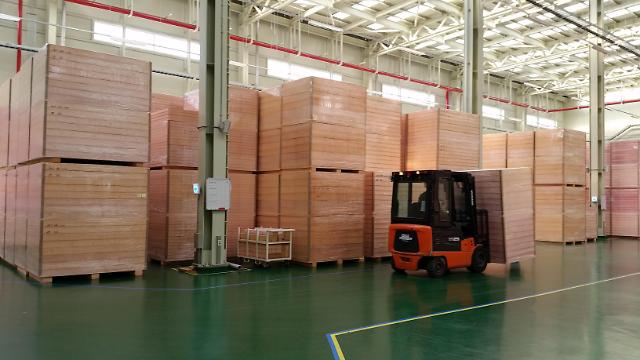
PF단열재가 공장내 가득히 적재돼 있다.[사진=이재영 기자]
©'5개국어 글로벌 경제신문' 아주경제. 무단전재·재배포 금지