여느 공장에서 들리던 곳곳의 기계음과 현장 직원들은 찾아보기 힘들었다. 그나마 눈에 띈 이들도 큰 움직임 없이 자동화시스템 조작 업무에만 열중했다. 6000여 개의 부품이 활용되는 현장에서 짐을 나르기 위해 분주한 직원도 없었다. 필요한 부품을 장치에 입력하고, LGV(Laser Guide Vehicle·자동운반장비)의 배송을 기다리면 됐다. 표준화‧자동화를 통해 단순반복 업무를 기계로 대체하고, 현장 직원의 수를 최소화시킨 미래 혁신 제조현장의 한 단면이었다.
생활가전을 생산하는 삼성전자 스마트공장을 탐방하기 위해 이날 광주광역시를 찾은 중소기업 대표만 500명이 넘었다. 스마트공장 도입을 앞두고 있는 중소기업이 대기업의 혁신 제조현장을 직접 체험하고, 벤치마킹하도록 지원하려는 목적에서 마련된 자리였다. 과거에도 몇몇 중소기업이 삼성전자 공장을 방문한 적은 있었지만, 대규모 체험단을 구성해 현장체험 및 교육을 실시한 것은 이번이 처음이다.
삼성전자 정밀금형개발센터는 약 2만6000m²(8000여 평) 규모의 공간을 단 250명이 통제했다. 이 중 120명은 금형설계 작업을 맡았고, 가공이나 조립에는 60여 명만 투입됐다. 사람 없이도 24시간 가동 가능한 이 공장은 2020년까지 인공지능 설계 등 고도화 작업을 마무리하면 투입인원을 180명으로 줄일 수 있다. 남은 인력은 다시 스마트공장 고도화를 위한 R&D 분야에 투입될 예정이다.
최성욱 삼성전자 스마트실행팀 상무는 “금형작업의 핵심은 금형설계의 표준화‧자동화다. 이 작업이 제대로 되지 않으면 생산시간이 길어지고, 평균 15%의 로스가 발생한다. 스마트공장에선 1% 미만의 불량률을 유지 중”이라며 “다른 공장에서 45일 걸리는 작업을 15일에 끝낸다. 2020년에는 9일로 줄이는 것이 목표”라고 설명했다.
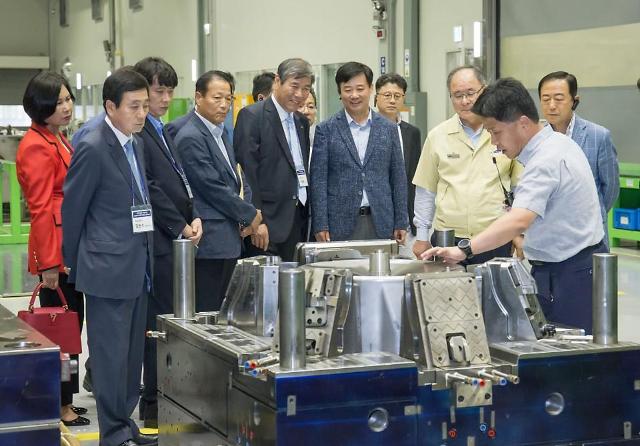
[12일 삼성전자 '그린시티' 를 방문한 중소기업 대표들이 ICT 기반 시스템이 적용된 최첨단 스마트공장 '정밀금형개발센터'를 둘러보고 있다.(사진=삼성전자)]
모든 가공‧조립 공정을 자동화하지는 못했지만, 사람이 하기 어려운 작업은 로봇 작업으로 대체하고 있다. 과거 700m에 달하던 컨베이어벨트 길이는 MTS 도입 후 획기적으로 줄었고, 작업시간도 200분에서 100분으로 단축됐다. 이곳에서는 세탁기로 빨래 한 번 돌릴 시간에 제품 한 대를 생산하고 있는 셈이다.
벤치마킹 교육을 받은 이주협 대륜산업 대표는 “삼성전자의 광주사업장 벤치마킹은 선진화된 스마트공장을 직접 본 소중한 기회였다. 스마트공장을 구축하면 제품생산과 재고의 효율적 관리가 가능하고 원가 절감에 도움이 될 것”이라며 “추진방향 설정부터 자금 부족, 시스템운영 부담 등을 고민하는 업체들에게 큰 도움이 되겠다”고 소감을 전했다. (광주)=신보훈 기자
©'5개국어 글로벌 경제신문' 아주경제. 무단전재·재배포 금지