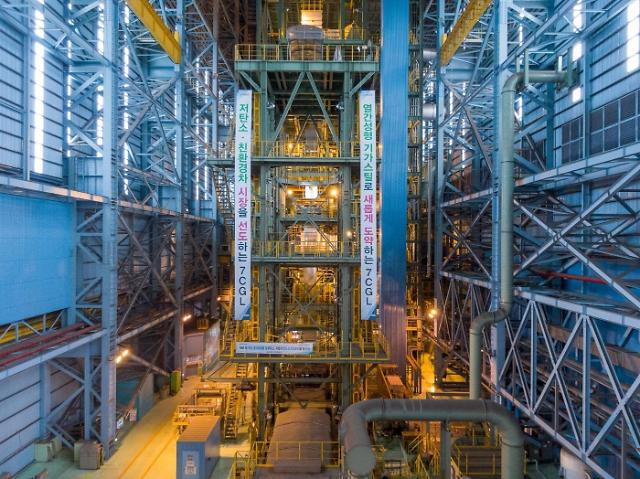
지구 반대편에서 온 원료를 보관하는 부두를 지나 7CGL(용융아연도금강판라인) 공장으로 향했다. 공장에 들어서니 높이 60m에 달하는 중장비 설비들이 가득했다. 제선·제강·압연을 통해 탄생한 강판은 이 공장에서 전처리·열처리·도금·조질압연·후처리·검사 과정을 거친다.
대표 제품은 '기가스틸'로 인장강도 1GPa 이상의 초고강도 강판이다. 1㎟ 면적당 100㎏ 이상의 하중을 견딜 수 있고 차량 부품 소재의 두께를 줄여 경량화가 가능하기 때문에 전기차에 적합하다. 포스코는 2021년 기가스틸 100만톤 생산체제를 구축하고 최대 0.5㎜ 두께까지 얇게 만들면서도 폭은 1650㎜까지 넓힐 수 있는 설비를 갖춰 자동차사들이 설계를 용이하게 할 수 있도록 지원하고 있다.
공장 안으로 들어서자 강판이 위에서 아래로 길게 널려져 있었다. 용접기 설비로 코일을 하나의 긴 제품으로 연결한 뒤 브러쉬로 철판의 표면을 닦아 불순물을 제거해줬다. 800도의 온도로 가열해 연질의 강판으로 만드는 작업이 이어졌다.
스킨패스밀(조질압연) 과정에서는 철판을 강한 압력으로 눌러 거칠기를 확보하고 평평하지 못한 부분을 펴줬다. 마지막으로 부식을 방지하기 위해 후처리 공정에서 용액이 도포됐다. 파란색 컨테이너박스 안에서는 수평검사대, 결함검출시스템 등을 통해 철저한 품질 검사를 하고 있었다. 공장 끝 한켠에는 완성된 은색 용융아연도금강판이 쌓여 있었다. 이곳에서 연 51만4000톤 규모로 생산된 자동차 강판은 전 세계 주요 완성차업체에 수출된다. 포스코 관계자는 "전 세계 자동차 판매량이 연간 8000만대 수준인 점을 감안하면 10대당 1대꼴로 포스코가 생산한 자동차 강판을 사용 중"이라고 말했다.
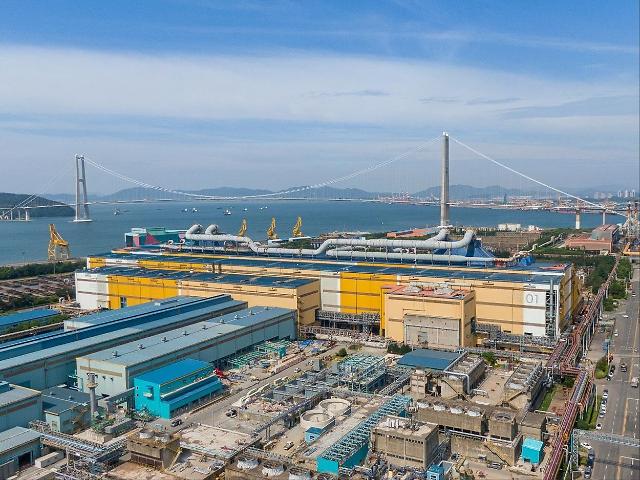
안형태 HyperNO능력증대TF팀장과 참석 기자들은 "안전 최고" 구호와 함께 엄지손가락을 들어올리며 건설 현장에 들어섰다. 생산 가능 두께를 최대 0.1㎜까지 낮출 수 있는 박물 전용 압연기(ZRM) 설비와 냉연설비들이 들어서 있었다.
포스코는 이번주부터 전기강판 설비 가동을 위한 시운전에 착수하고 오는 10월 준공에 돌입한다. 규모는 연산 40만톤으로 2025년 완공된다. 전기강판 40만톤은 전기차 500만대의 구동모터코어를 만드는 데 쓸 수 있는 양이다.
전 세계적으로 전기강판을 생산하는 곳은 중국 바오산철강, 일본제철 등 14개사에 그친다. 이번 광양 공장이 완공되면 포스코의 생산 능력은 무방향성 전기강판 40만톤을 포함해 총 113만톤으로 늘어나게 돼 전기차 및 고효율 가전 시대에 적극 대응할 수 있을 것으로 기대되고 있다.
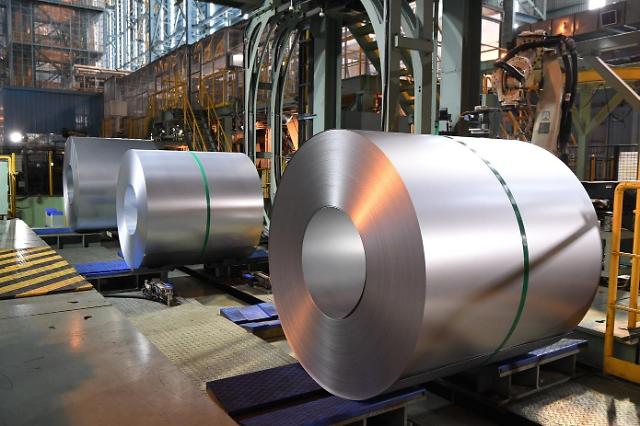
©'5개국어 글로벌 경제신문' 아주경제. 무단전재·재배포 금지