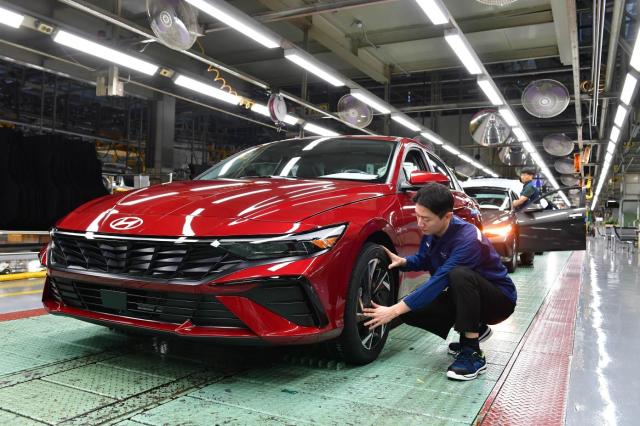
울산공장은 아이오닉 5와 싼타페, 팰리세이트, 투싼, 넥쏘, GV60·70·80, 코나, 포터, G70·80·90 등 17대의 최고 차종을 양산하며 수출 전진기지 역할을 톡톡히 하고 있다. 지난해 이 공장이 생산한 차량 142만4141대 중 66%가 수출 물량이다.
지난 18일 찾은 울산 3공장에서는 아반떼, 베뉴, 코나, i30 생산에 한창이었다. 자동차의 제조 공정은 프레스-차체-도장-의장 등 크게 4단계로 나눠지는데 3공장에서는 의장 공정이 숨가쁘게 진행되고 있었다. 3공장의 연간 생산량은 36만7000대다. 특히 지난해 8월부터 다차종 생산 시스템이 시범 적용되면서 최대 10개의 차종을 동시에 생산할 수 있게 됐다. 기계만 가득할 줄 알았던 공장에는 직원들로 붐볐다. 의장라인은 정교한 작업이 필요한 공정이기 때문에 90% 수작업으로 이뤄진다.
작업자들은 컨베이어벨트 위 아반떼의 도어를 드릴로 탈거하는 데 여념이 없었다. 내부에 2만여 가지 부품을 장착하는 작업을 수월하게 하기 위해서다. 문은 서브라인에 옮겨져 마지막에 재장착된다. 와이어링이나 케이블 같은 전장 계열 부품을 비롯해 제동 부품, 구동 부품, 내·외부 인테리어 부품이 순차적으로 장착된다. 전자 부품에 소프트웨어를 입력해주는 코딩 작업도 이곳에서 이뤄진다.
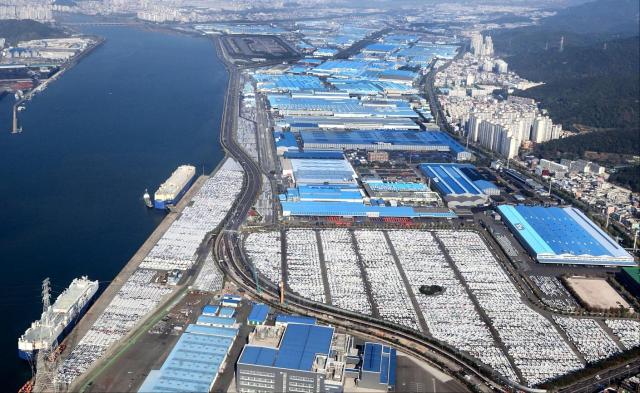
현대차의 자동차운반선은 제품을 최대한 많이 적재하면서도 손상을 최소화하는 데 중점을 둔다. 배 안에는 12~15개의 데크를 이용해 층을 나눠 자동차를 선적한다. 데크는 차 크기에 따라 위아래로 움직여 공간을 확보한다. 배는 시속 20km로 천천히 움직이지만 흔들릴 경우 자동차 제품들 간 충돌을 막기 위해 차에 갈고리를 단 모습도 보였다. 갈고리는 2000kg의 무게를 버틸 수 있다. 하얀색의 부직포를 차 곳곳에 붙여 차를 새의 배설물로부터 보호하기도 했다.
현대차는 올 판매 목표를 상향조정하면서 공장은 더욱 바쁘게 돌아갈 전망이다. 현대차의 올해 글로벌 목표 판매량은 지난해보다 10% 증가한 432만대다. 오는 2025년 23만4700㎡(약 7만1000평)의 부지의 전기차 전용 공장까지 완공되면 울산공장은 다양한 차세대 미래차를 양산하는 국내 미래차 생산의 대표 거점이 될 것으로 기대된다.
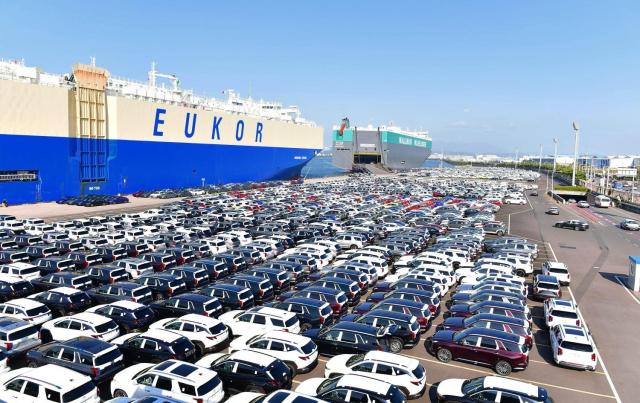
©'5개국어 글로벌 경제신문' 아주경제. 무단전재·재배포 금지